Top 7 Supply Chain Master Data management Software
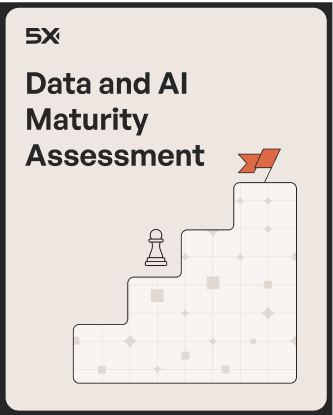
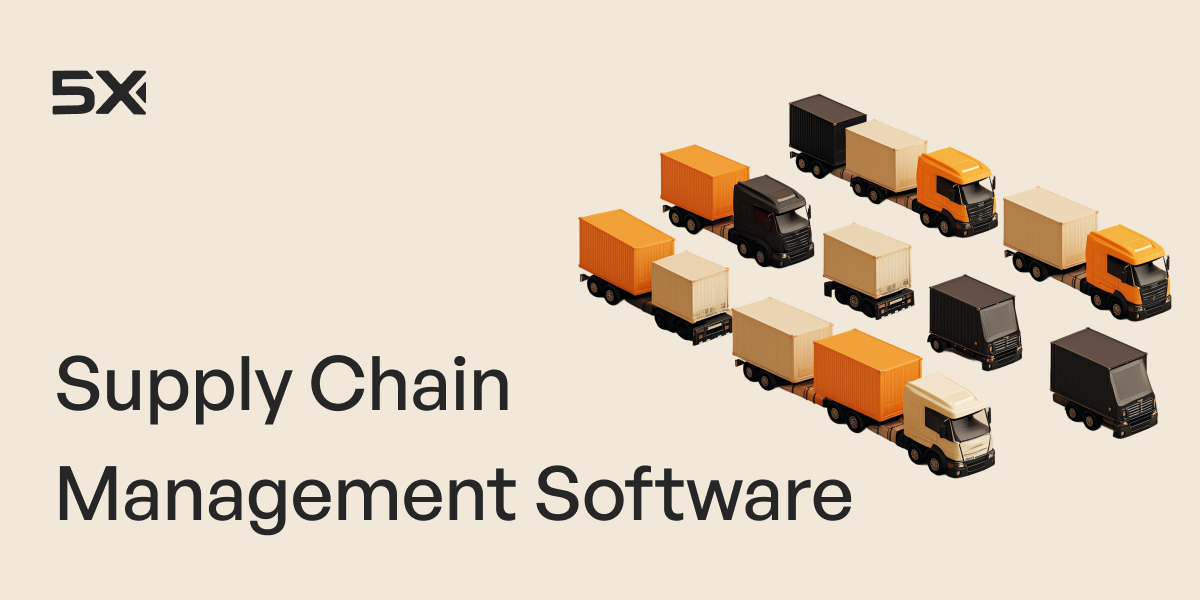
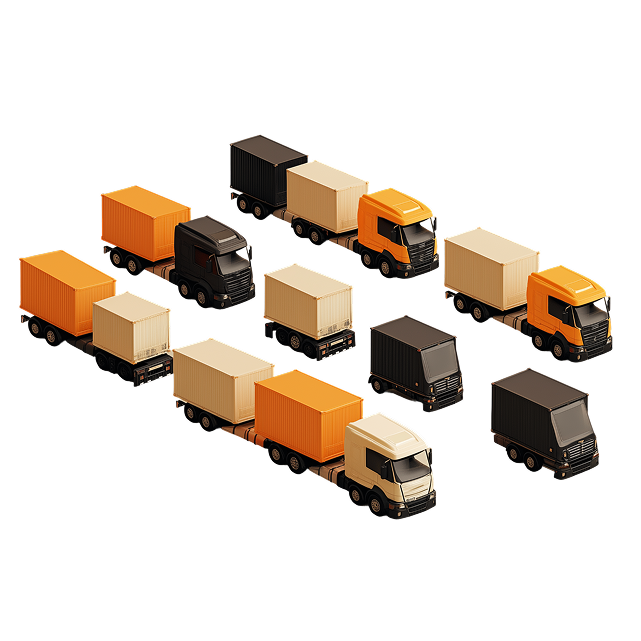
Table of Contents
TL; DR
- Most supply chains break not from poor tools but from messy, mismatched master data across systems
- MDM software unifies core records like SKUs, suppliers, and warehouse data across systems in real time.
- Cleaner data reduces stockouts, improves forecasts, and saves hundreds of manual hours
- Tools like 5X, Semarchy, and Profisee make MDM faster and easier for ops, not just IT teams
- The right MDM setup turns your data from a liability into a supply chain advantage
Most supply chain leaders already understand the cost of fragmented data: mismatched SKUs, conflicting supplier records, and inventory blind spots that stall decisions. What’s less clear is which MDM platform will align with your existing stack, deliver operational value fast, and scale with minimal disruption.
Do you need a robust, enterprise-grade system or a leaner platform that delivers clarity without months of integration? Will the tool be operable by business users, or will it require dedicated IT resources to maintain?
This guide is built for decision-makers evaluating MDM in real-world conditions. We break down the strategic trade-offs between leading platforms, highlight who they’re best suited for, and offer a clear lens on time-to-value, flexibility, and governance depth.
What is a supply chain master data management software?
At its core, supply chain MDM is the engine room of data clarity. Gartner defines MDM as “a technology-enabled discipline in which business and IT work together to ensure uniformity, accuracy, stewardship, semantic consistency and accountability of an enterprise’s official shared master data assets.” In practice, MDM ensures every stakeholder in your supply chain—procurement, warehouse, finance, logistics, even customer service—is working with the same accurate, up-to-date data.
So, what exactly counts as “master data” in supply chain terms? It’s the core, non-transactional information that every process relies on, for example:
- Products: SKUs, dimensions, units, classifications
- Suppliers: Vendor names, contacts, payment terms
- Customers: Billing and shipping info, contracts, service levels
- Locations: Warehouse IDs, zones, route maps
- Logistics: Carriers, transit times, shipping constraints
Now imagine all that data stored across seven different platforms, in nine different formats, updated by a dozen different people, with no synchronization. That’s the daily reality for most supply chain teams and it’s exactly why MDM software exists.
Why master data matters in supply chain operations
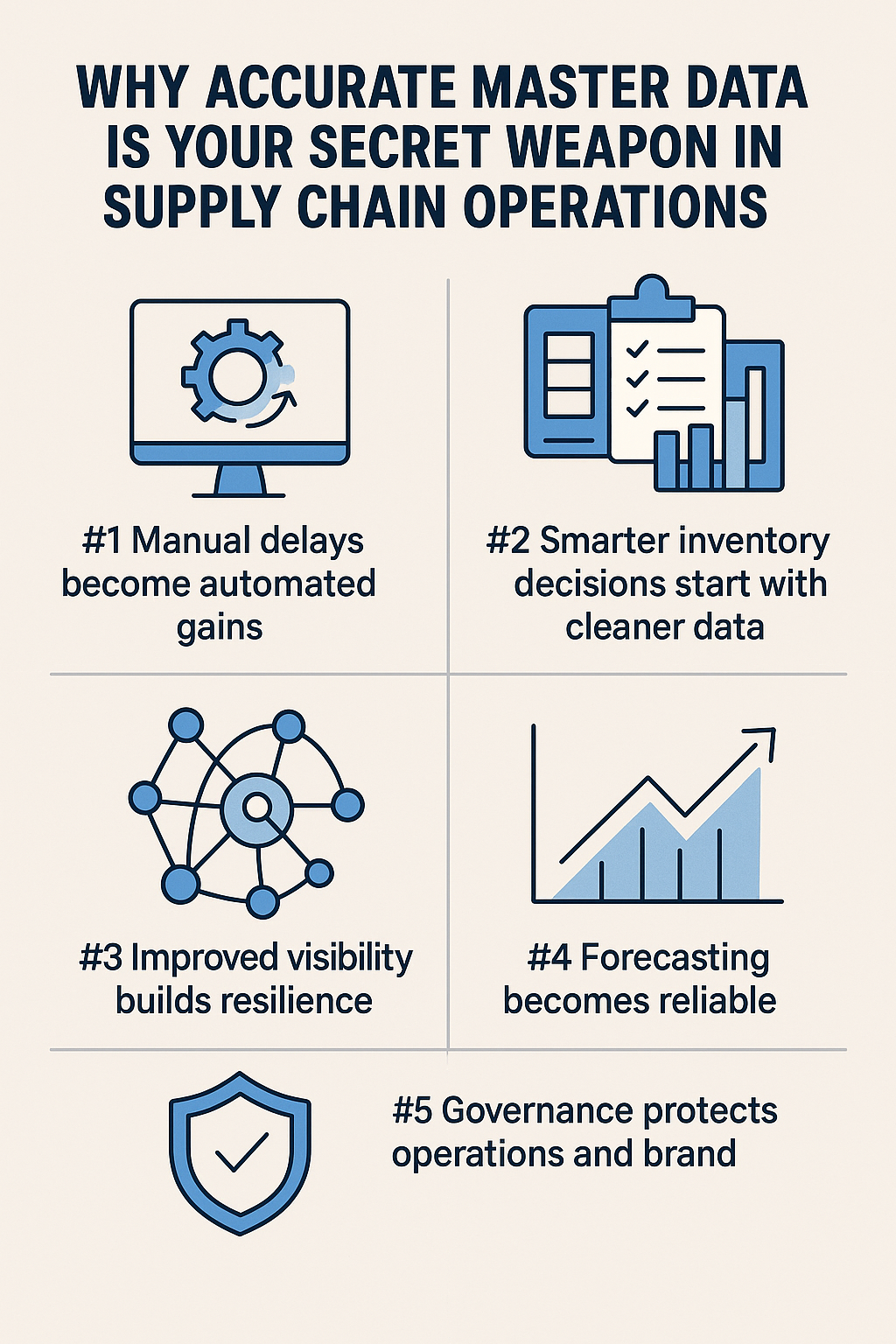
When your supply chain data is inconsistent, duplicated, or buried in silos, it creates bottlenecks everywhere. Your team spends more time checking data than using it. Orders get delayed due to data mismatches. Stock levels swing wildly between surplus and shortages. Vendor coordination feels like a guessing game. That’s the real cost of bad master data; it slows you down just when you need to move fast.
By contrast, cleaning up and unifying your master data can unlock huge improvements. Let’s look at five big ways master data management can boost supply chain performance (with real examples):
#1 Manual delays become automated gains
Without a single source of truth, teams are forced to jump between tools and spreadsheets just to answer basic questions. With modern MDM, much of that manual reconciliation disappears.
For example, restaurant chain Cupbop used 5X’s data platform to centralize its supply chain data and automate reporting. The result? They reclaimed over 300 hours every month that were previously spent manually reconciling reports across systems.
5X has transformed the way we work. The automated data collection & reporting saves us 300 hours+ / month in manual work. And the insights help us identify & double down on activities that boost store revenue.
Kevin Santiago, President, Cupbop
Cupbop reduced food waste by 25% and saved 300 man hours/month via automation
#2 Smarter inventory decisions start with cleaner data
Poor master data makes it almost impossible to maintain optimal inventory. If product info, BOMs, or warehouse data are inconsistent, your planning models will be off. Standardizing these through MDM leads to more accurate inventory levels and less waste.
In Cupbop’s case, better data led to a 25% reduction in food waste across their stores. In supply chains at scale, avoiding just a few percentage points of overstock or stock-out can mean millions in savings.
#3 Improved visibility builds resilience
Unfortunately, many companies have very limited visibility into their supplier networks beyond the first tier. Only about 48% of supply chain leaders have visibility into Tier-1 suppliers, 21% into Tier-2, and just 2% into Tier-3. This is a recipe for nasty surprises when a disruption strikes.
MDM helps by unifying data across procurement, supplier management, and risk systems to give an end-to-end view of your supply network.
#4 Forecasting becomes reliable
Accurate forecasting depends on consistent, trustworthy data about products, sales, and inventory. Many companies suffer frequent stock-outs or excess inventory because their underlying data is fragmented or outdated. When master data is cleaned up, forecasting models suddenly have a solid foundation.
Real-world case study
In a healthcare supply program in Tanzania, introducing better data systems (a form of master data and logistics management) reduced medication stock-out rates from 32% to 23% and also lowered the cost per unit dispensed from 58% to 50%.
That kind of improvement—nearly a third fewer stock-outs—only happens when data is clean, consistent, and up-to-date.
#5 Governance protects operations and brand
Your data feeds contracts, compliance reports, audits, and recall processes. When your records are accurate and traceable, you reduce legal risks and build trust with partners and regulators. Conversely, poor master data (like incorrect specifications or missing compliance info) can lead to audit findings, regulatory fines, or shipment rejections.
Companies with strong MDM practices have clearer visibility into their suppliers, products and customers, leaving them better positioned to handle disruptive events or changes in the regulatory environments.
Also read: How to Improve your Supply Chain Process using AI
7 Best supply chain master data management software in 2025
Choosing the right MDM solution depends on your company’s size, tech ecosystem, and priorities. Below we review seven leading tools (in no particular order) that supply chain teams are using for master data management in 2025.
We’ll highlight what each does best, and where each has limitations.
1. 5X data platform: Fast, operational clarity
5X offers a unified data platform built to help teams clean, govern, and operationalize their data. It brings together master data from systems like ERPs, WMS, CRMs, and vendor platforms into one place.
The platform is designed to surface data issues quickly, apply governance rules automatically, and give users real-time dashboards that reflect current supply chain realities.
Users can go from scattered spreadsheets to unified dashboards in days. 5X also adds a conversational AI layer to highlight inconsistencies, gaps, or anomalies in natural language.
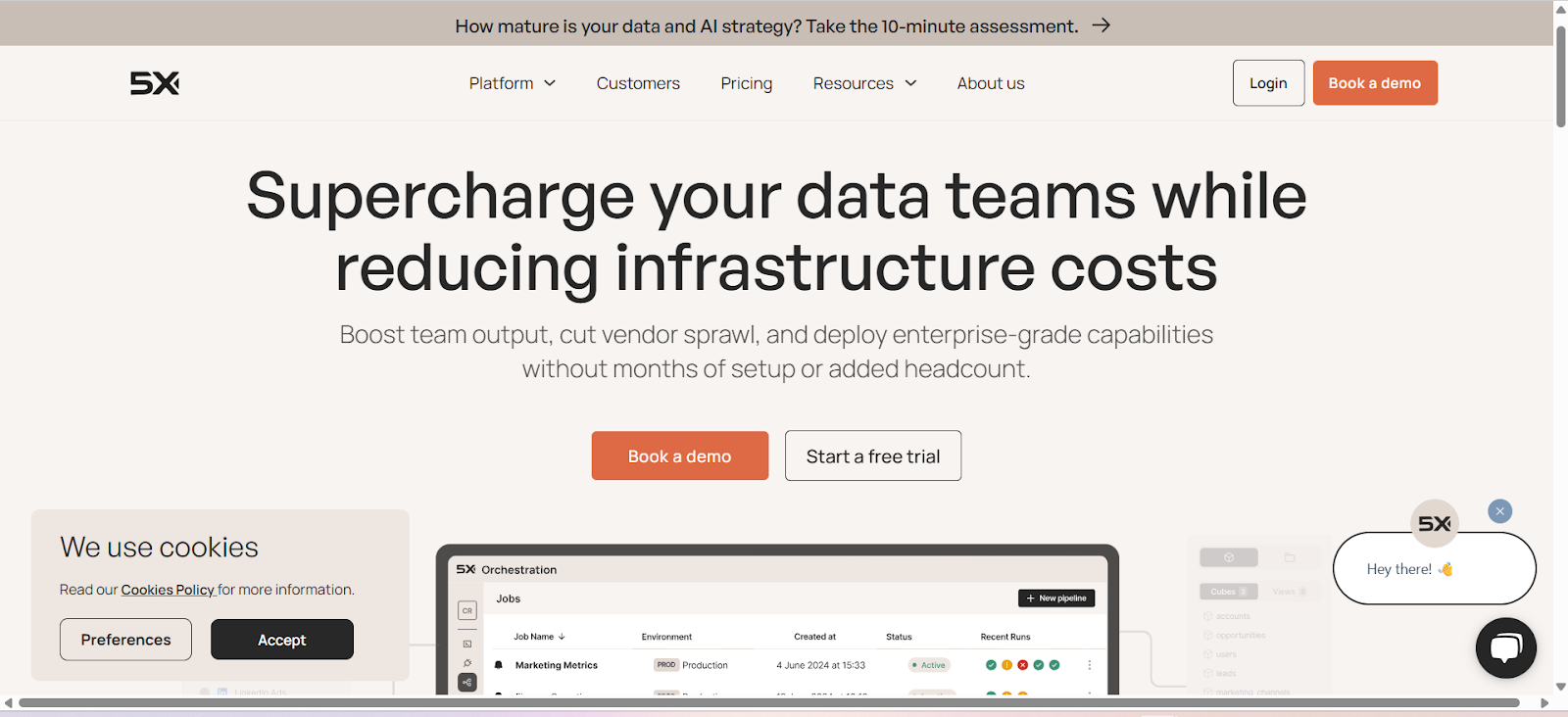
What stands out
- Built for speed and ease-of-use, even for non-technical users
- Combines data onboarding, cleansing, governance, and visualization in a single no-code experience
- Addresses the “dark data” challenge by helping teams make sense of fragmented, underused data
- Recognized by G2 for exceptional usability, support, and return on investment
Rating: 4.9/5 on G2
Best for: Companies looking to unify supply chain data fast without heavy IT involvement
Pricing:
- Free plan: up to 1 million rows and 1 TB scans
- Starter: $999/month
- Business: Custom pricing
2. Semarchy xDM: Flexible and scalable data unification
Semarchy xDM offers a configurable master data hub that supports domains critical to supply chains—products, suppliers, locations, assets, and pricing. Users appreciate its metadata and hierarchy management, data lineage tracking, and model-driven configuration that adapt to changing business needs.
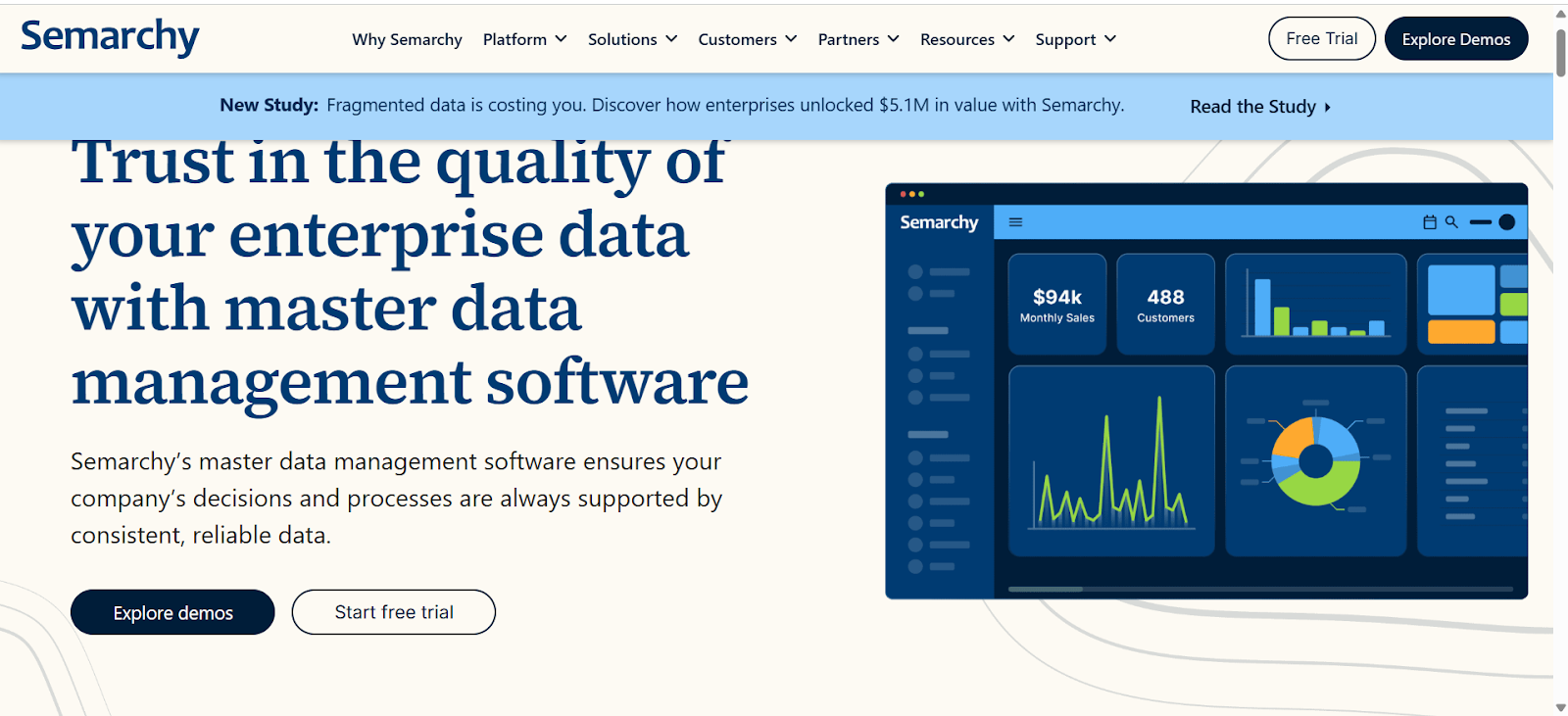
What stands out
- No-code model building and governance features make it accessible to business users
- Strong real-time synchronization via APIs ensures data is always fresh
Considerations
- Custom setups can take time and require planning
- Costs may increase significantly as usage scales
Rating: 4.8/5 on G2
Best for: Large businesses with diverse and evolving data systems
Pricing: Not publicly listed. Contact for quote
3. Profisee: Seamless integration with Microsoft environments
Profisee is a cloud-native MDM platform that has carved out a niche as the go-to solution for Microsoft-centric companies. It’s certified for Azure and designed to work natively with tools like Azure Data Factory, Purview, and Power BI.
Supply chain teams use Profisee to consolidate product, supplier, or customer data while staying within familiar Microsoft interfaces. It supports multi-domain MDM and offers a decent set of data quality, matching, and governance capabilities.
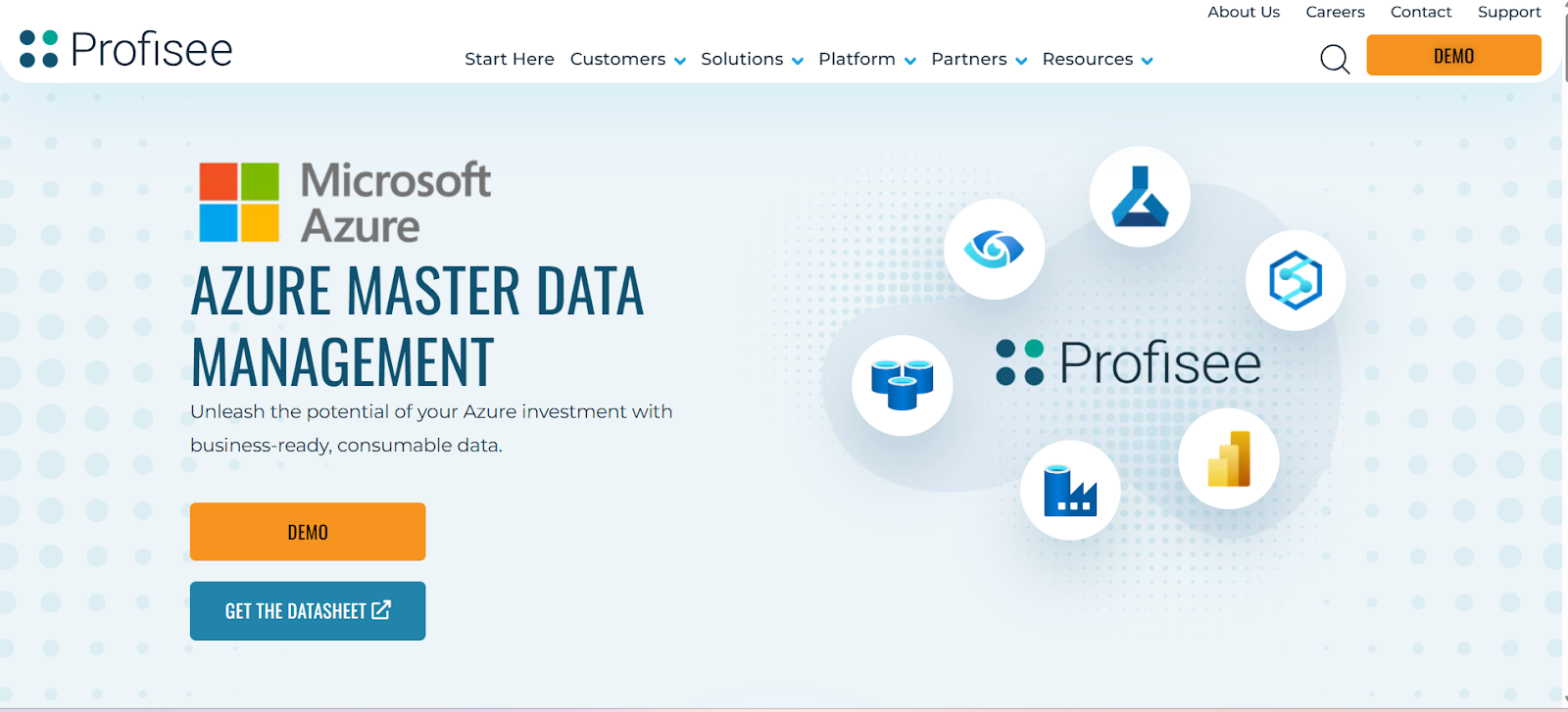
What stands out
- Fast setup and low cost of ownership
- Highly responsive support credited for speeding up time to value
Considerations
- Analytics and advanced modeling capabilities can be basic
- Customization options are limited compared to enterprise tools
Rating: 4.3/5 on G2
Best for: Organizations using Dynamics 365, Azure SQL Server, or Power BI
Pricing: Not publicly listed; quote-based
4. Informatica MDM: Advanced matching and 360-degree master data views
Informatica is a longtime leader in data management, and their MDM solution is known for very powerful entity resolution capabilities. Using machine learning and rules, Informatica MDM can match records from dozens of sources with high accuracy, even when there’s no common key.
It can manage multiple domains (supplier, product, customer, etc.) and create 360-degree profiles (for example, a supplier profile that pulls together certifications, performance scores, risk indicators, etc., from multiple systems). Informatica MDM is available as a cloud service and can integrate with the rest of Informatica’s data quality and integration tools.
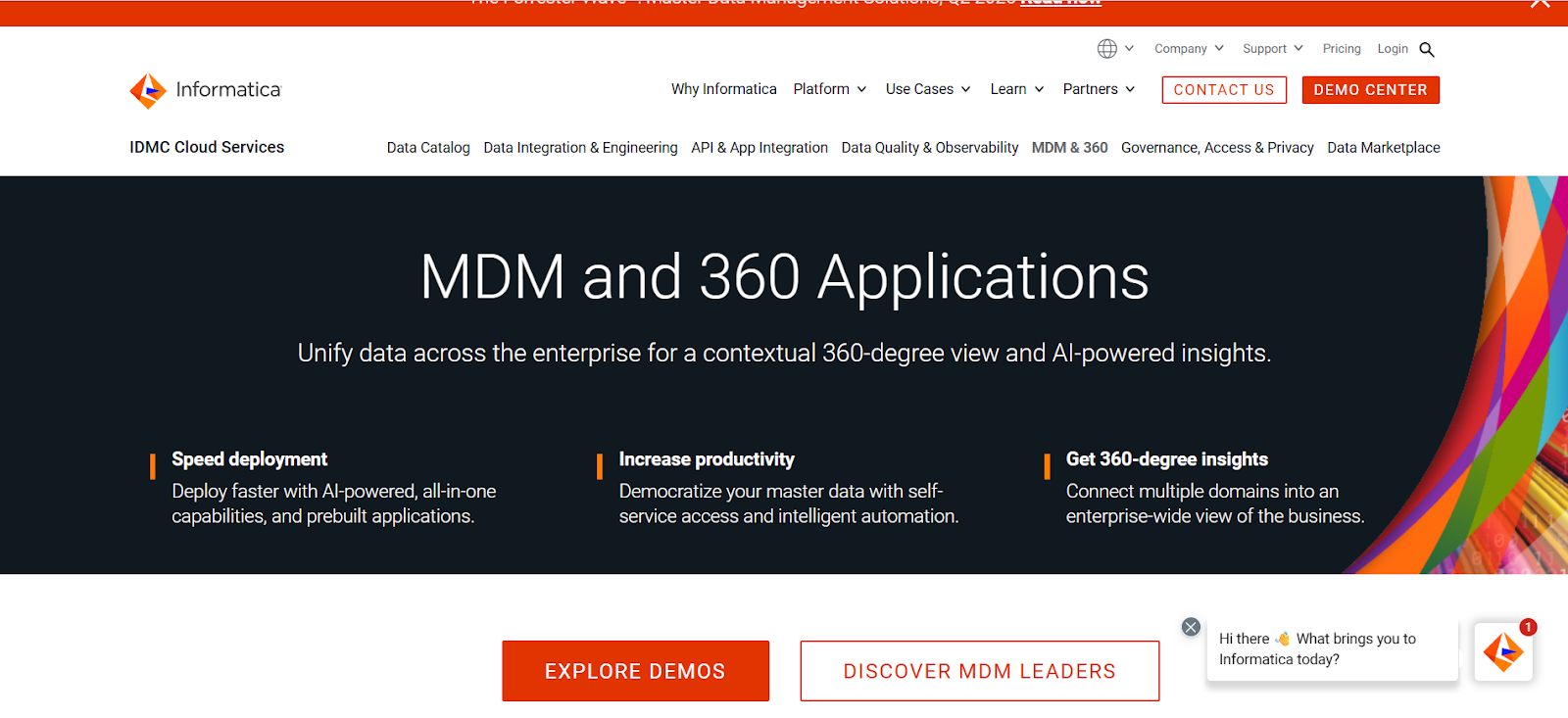
What stands out
- Highly effective deduplication and smart matching capabilities
- Flexible domain support for complex supply chain contexts
Consideration
- Requires a high level of technical expertise to configure and maintain
- Implementation timelines can be long and resource-heavy
Rating: 4.2/5 on G2
Best for: Large enterprises requiring strong data matching and identity resolution
Pricing: Not publicly listed; based on usage via the IDMC platform
5. TIBCO EBX: Unified control across master, reference, and hierarchy data
TIBCO EBX (formerly from Orchestra Networks) is an all-in-one data management platform that covers MDM, reference data management, and metadata management in one package. It’s quite flexible: you can model any domain (products, suppliers, finance, etc.) and manage not just the master records but also code lists, hierarchies, and governance workflows all in the EBX system.
Users highlight its strong collaborative workflows (for example, approving a new master record or changes through a governance process) and the ability to manage complex data relationships.
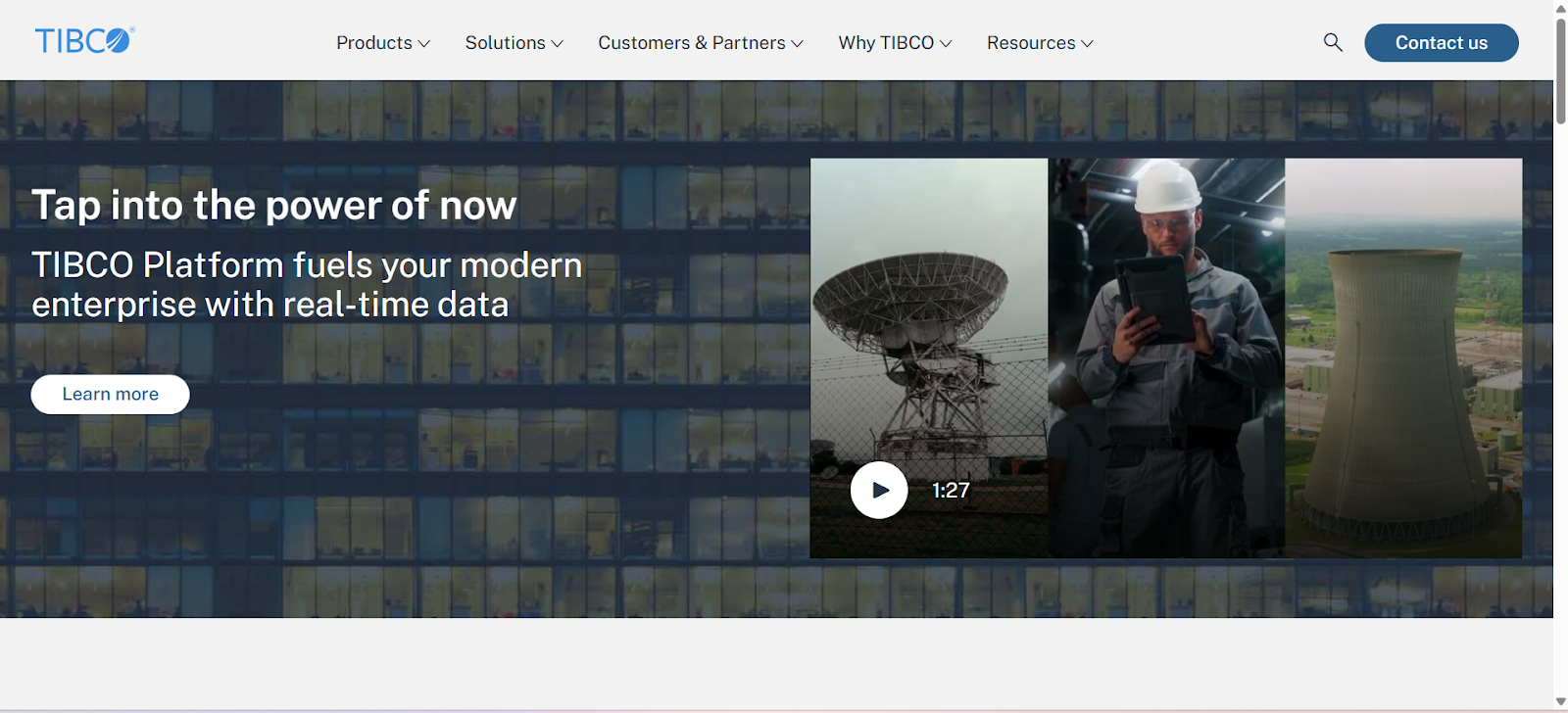
What stands out
- Highly flexible for model-driven, domain-agnostic data management
- Strong metadata and lineage features that support governance
Considerations
- Non-technical users may struggle with initial configuration
- Implementation requires involvement from IT and data architects
Rating: 4.4/5 on G2
Best for: Enterprises needing a unified platform for master, reference, and hierarchical data
Pricing: Not fully public; typical annual cost around $52K, entry pricing varies
6. Oracle EDM Cloud: Streamlined enterprise data management
Oracle EDM Cloud offers a unified platform for managing supply chain, finance, and logistics data. For supply chain, it can unify master data across Oracle ERP, supply chain, and financial applications.
Oracle EDM emphasizes simplified change management—e.g., if you add a new product or reorganize cost centers, EDM provides a central place to make that change and push it out to all connected Oracle systems. It’s also used for what Oracle calls “dimension management,” which is keeping hierarchies (like product category structures, organizational hierarchies, etc.) consistent across systems.
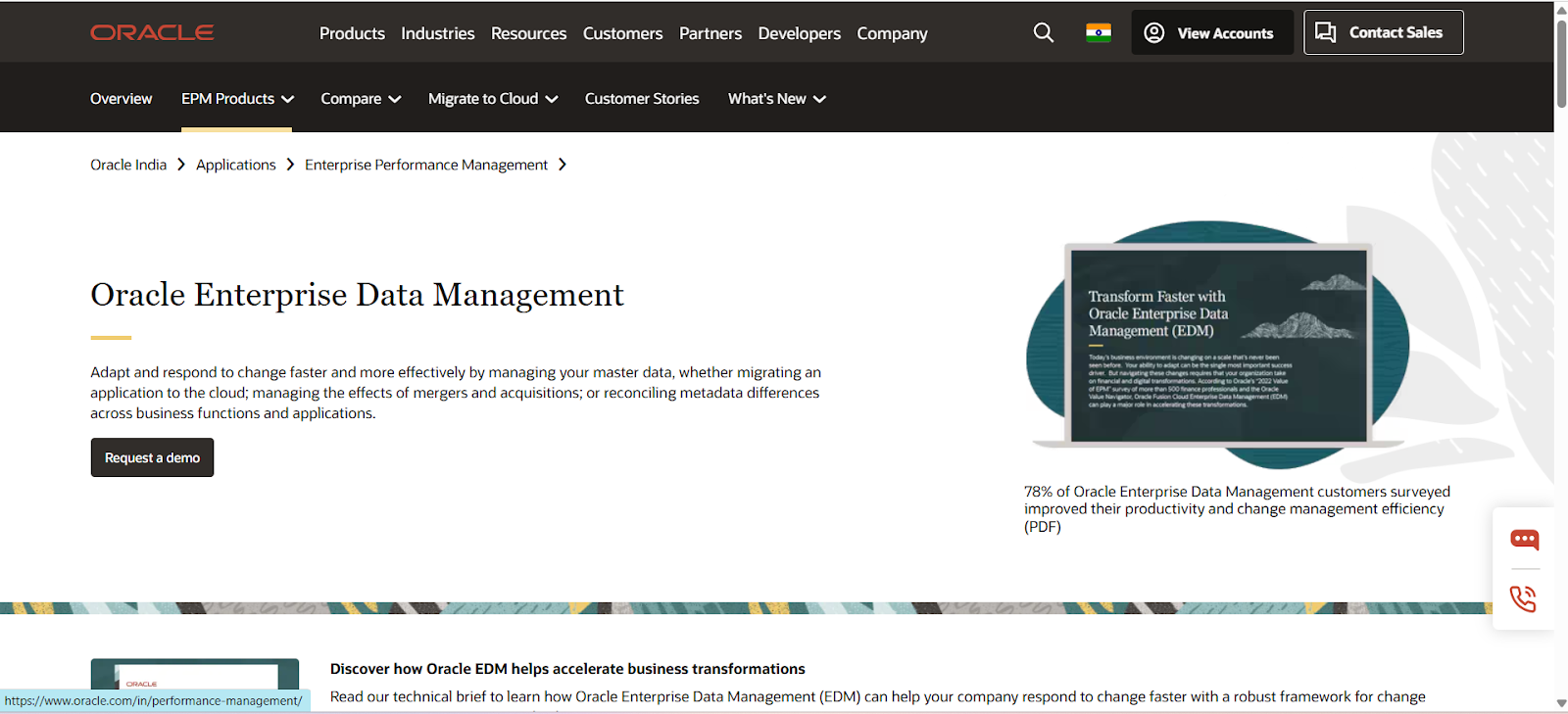
What stands out
- Accelerates multi-domain workflows with streamlined interface
- Enables quick access to accurate data for decision makers
Considerations
- Primarily optimized for Oracle Cloud and Fusion apps
- Integration outside Oracle ecosystem may require custom development
Rating: 4.1/5 on G2
Best for: Businesses using Oracle Cloud or Fusion apps for master data needs
Pricing: Limited public info; reported rates include $1,500/1,000 records/month or $12/employee/month
7. SAP Master Data Governance (MDG): Built-in governance for SAP-centric organizations
SAP MDG provides centralized governance, workflows, and validation rules natively within SAP environments. It offers pre-built governance for key objects like material master (products), business partner (customers/suppliers), and financial reference data.
MDG runs on the SAP platform, which means it uses the familiar SAP interface and workflows. Data stewards can use MDG to create or change a master record with a governed process. For example, a new supplier request can trigger an approval workflow and validations before the supplier is created in the system. All changes are versioned and auditable.
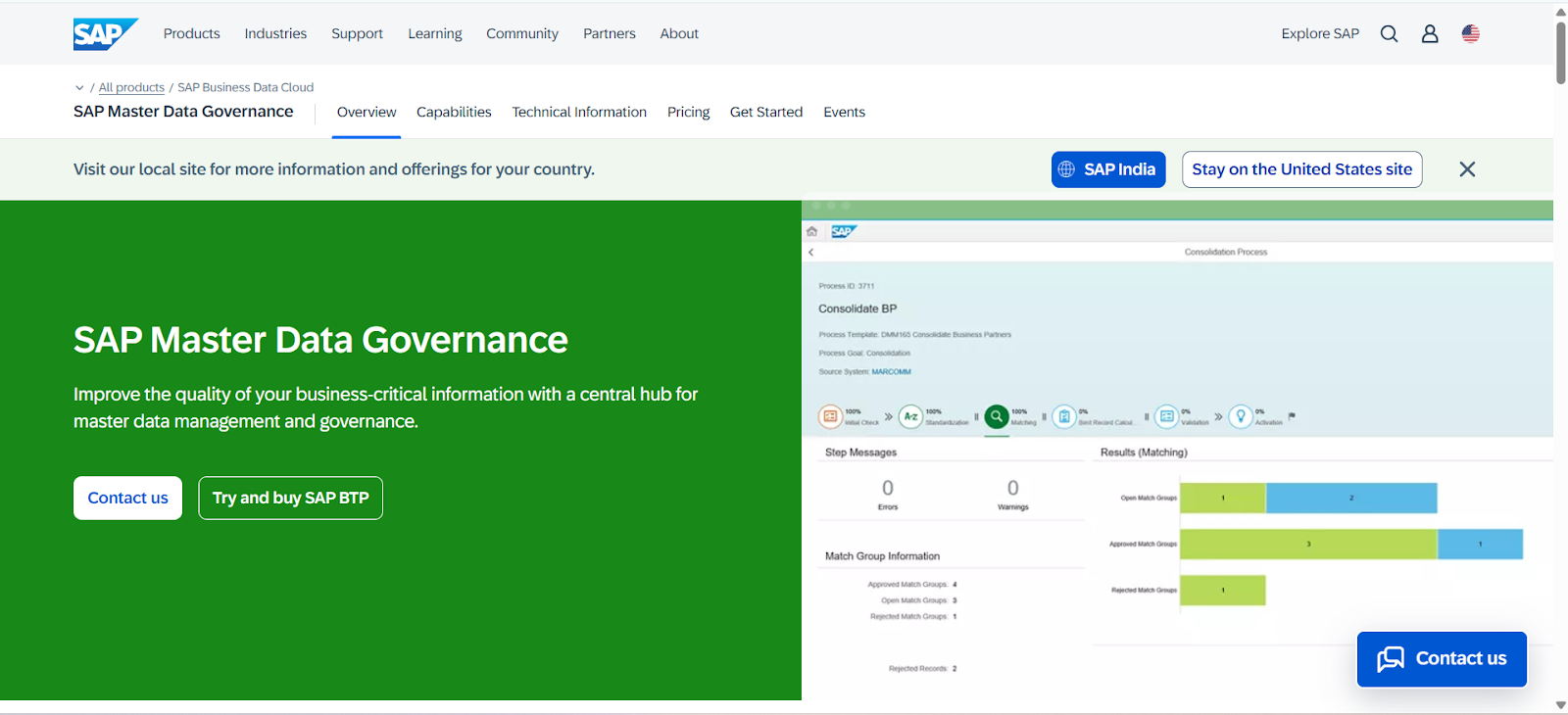
What stands out
- Deep ERP alignment with consistent policy enforcement across SAP modules
- High user satisfaction and efficient data stewardship processes
Considerations
- Best suited for companies already using SAP ERP or S/4HANA
- Complex integration and setup process for non-SAP environments
Rating: 4.4/5 on G2
Best for: Organizations operating in SAP ERP or S/4HANA ecosystems
Pricing: Starts at $87 per month for each block of 5,000 objects (annual contract)
How to implement MDM in supply chain operations
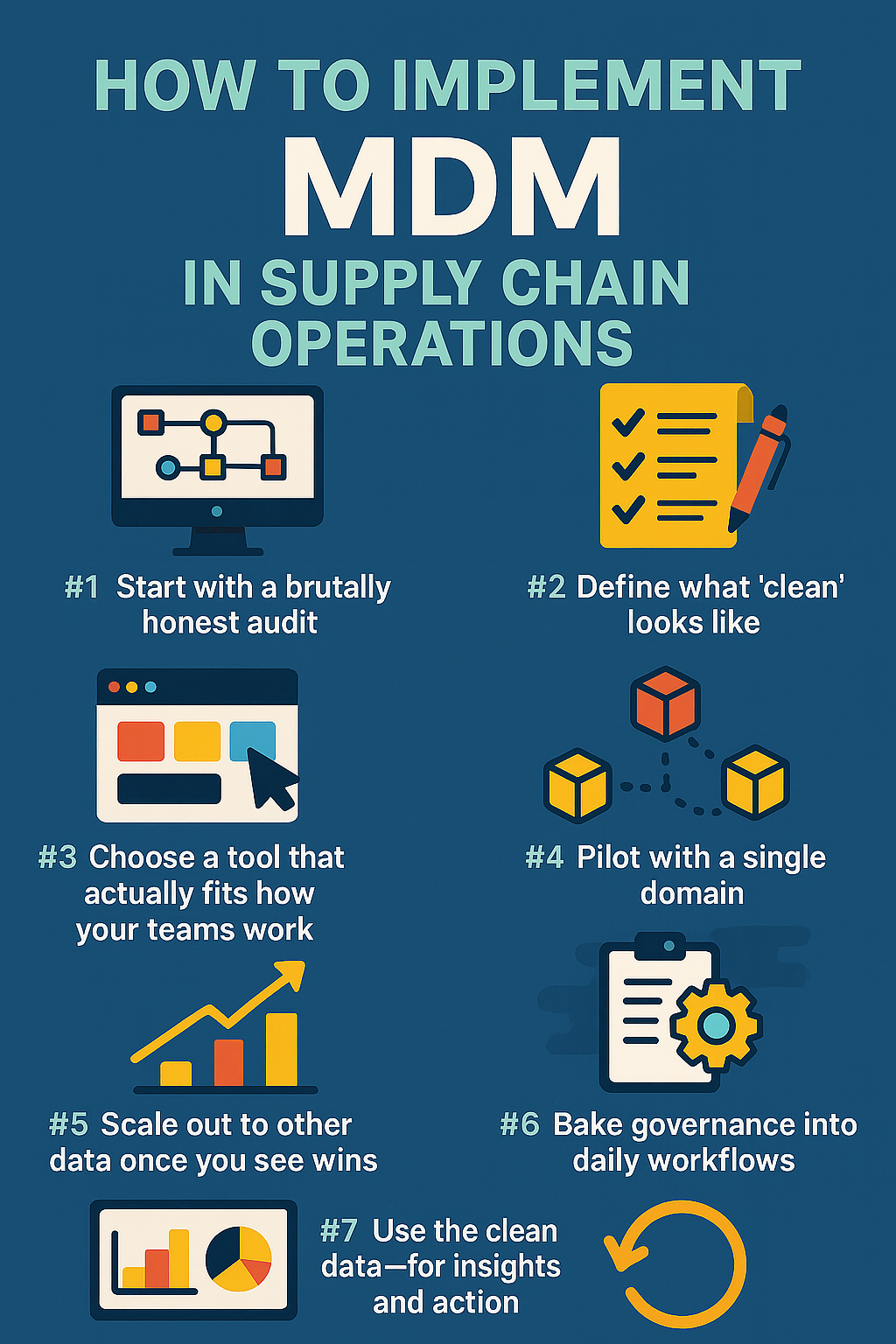
Implementing MDM doesn’t have to be a never-ending IT project. If you're trying to fix your data chaos and make your supply chain actually run smoother, here's how to do it.
#1 Start with a brutally honest audit
Map out where all your master data lives right now. ERP, warehouse management system, procurement spreadsheets, supplier databases, etc. Trace how data flows (or doesn’t) between them. Document the points where things break down.
You might find, for example, that vendor names are entered four different ways across systems, or that product codes between your ERP and e-commerce site don’t line up, or that two systems have conflicting “source of truth” for inventory levels.
This data audit is your baseline. You can’t fix what you can’t map. It will also help build the case for why MDM is needed (seeing the messy reality in detail is often an eye-opener for leadership).
#2 Define what “clean” looks like
Before rushing to load data into a new tool, spend time on your data standards and governance policies. What does a “golden record” look like for each domain? Decide which attributes are mandatory and who is responsible for them.
For example, define that “Supplier” records must have a unique Tax ID, a standardized company name, an assigned category, etc. Establish who can create or update each master data type (data owner stewardship). Also set rules like how often data should be reviewed or refreshed.
This doesn’t have to be over-engineered; start with practical rules to prevent the known issues you saw in step 1. The idea is to stop chaos from creeping back in after you clean up.
Tip: This is where many teams stall because defining standards feels abstract. Using a modern tool can help here. For instance, a platform like 5X lets you quickly configure rules and see the impact (e.g., it will instantly flag records violating a rule), without needing a lot of custom coding.
#3 Choose a tool that actually fits how your teams work
Not all MDM solutions are the same. Some are built for data architects to manage behind the scenes; others are designed for business users to operate day to day. Be realistic about your team’s skills and the level of IT support available.
If you need to unify product SKUs and supplier lists quickly and don’t have a big IT team, a lighter-weight or managed solution (like 5X or Profisee) might be better than a toolkit that takes months to stand up.
On the other hand, if you have very specialized requirements and an IT team ready to customize, an enterprise tool (like Informatica or SAP MDG for SAP shops) could be worth the investment.
Ask this question: “How long until we see value?” If a vendor’s answer is in quarters or years (and requires armies of consultants), it might not be the right fit for an organization looking for quick wins.
Many mid-sized firms opt for a more agile approach—for example, 5X can get your data unified in days, not months, by handling a lot of the heavy lifting (integration, cleaning, etc.) for you.
Also read: Top 5 master data management software in 2025
#4 Pilot with a single domain
Don’t boil the ocean at first. Pick one master data domain that is causing pain, commonly either product data or supplier data in a supply chain context, and focus your initial MDM effort there.
For instance, start by cleaning up product master data: standardize all the units, categories, and SKUs, and sync that between your ERP, your warehouse system, and your forecasting tool.
Measure the impact: Does reporting speed up? Do people trust the numbers more? Maybe you notice inventory decisions improve because everyone sees the same item availability data. Success in one domain will not only deliver immediate benefits, it will also create momentum and lessons you can apply to the next domain.
#5 Scale out to other data once you see wins
After a successful pilot, expand your MDM program to other areas like suppliers, customers, or locations. This is where you implement more automation: set up batch or real-time data integration so that, say, new supplier records from your procurement system automatically flow into the MDM hub and out to all subscribing systems.
Implement data quality checks (e.g., duplicate detection, completeness checks) for each new domain. It’s helpful at this stage to also add monitoring dashboards. For example, a dashboard showing the number of duplicate records over time, or fill rates of key fields, or how quickly data changes are being approved and applied.
#6 Bake governance into daily workflows
MDM is not a one-time cleanse; it’s an ongoing discipline. But “governance” need not be a scary word. The goal is to incorporate basic data ownership and review steps into the existing processes.
For example, assign someone from the supply chain or ops team as the data steward for each domain. They don’t have to be technical, they just need to care about the data’s accuracy and get notified when something needs attention.
Set up simple Service-Level Agreements like “any new supplier must be validated within 48 hours” or “when a field value is changed, an alert goes to the data steward to approve if critical.”
Modern MDM tools support creating these workflows and notifications so that maintaining data quality is part of the routine. The idea is to prevent errors at the source (e.g., catch that a new warehouse code is entered with the wrong format before it wreaks havoc downstream) without causing too much friction.
#7 Use the clean data for insights and action
Ultimately, MDM is a means to an end: better decision-making and streamlined operations. Once your core data is centralized and trustworthy, put it to work. Merge master data with transactional data to find insights.
For example, with unified data you can analyze spend by supplier across the company (because all supplier records are linked to one master) and perhaps negotiate better volume discounts. Or you can build more accurate demand forecasts because your sales, inventory, and product data are all aligned.
Maybe you set up an alert that warns you of a potential stock-out before it happens by correlating lead times, current stock, and open orders—something that was hard to do when data lived in separate silos.
A good MDM system (or integrated data platform like 5X) will often provide reporting and analytics layers or easily feed into BI tools. For instance, 5X allows building dashboards on top of the unified data without needing separate BI software, and even non-technical users can query the data using natural language.
#8 Rinse, refine, repeat
MDM isn’t a one-and-done thing. New suppliers arrive. New products launch. Data rules shift.
Schedule monthly reviews of data health metrics. Adjust your standards. Add workflows. And keep building on what works.
Why 5X gives you control over your supply chain data
Your supply chain is only as agile as the data powering it. And most operations are still stuck wrangling spreadsheets, reconciling systems that don’t talk, and reacting too slowly to change. Master Data Management is critical, but traditional MDM tools are often complex, slow to implement, and narrowly scoped.
That’s where 5X stands apart.
Unlike rigid MDM suites, 5X is a modern data platform that unifies your ERP, WMS, CRM, and logistics data in one place fast.
Whether you're cleaning up supplier records, syncing product SKUs, or forecasting with real accuracy, 5X gives you control without the complexity. You get the governance of MDM, the agility of BI, and the clarity of a unified platform.
Building a data platform doesn’t have to be hectic. Spending over four months and 20% dev time just to set up your data platform is ridiculous. Make 5X your data partner with faster setups, lower upfront costs, and 0% dev time. Let your data engineering team focus on actioning insights, not building infrastructure ;)
Book a free consultationHere are some next steps you can take:
- Want to see it in action? Request a free demo.
- Want more guidance on using Preset via 5X? Explore our Help Docs.
- Ready to consolidate your data pipeline? Chat with us now.
Get notified when a new article is released
How retail leaders unlock hidden profits and 10% margins
Retailers are sitting on untapped profit opportunities—through pricing, inventory, and procurement. Find out how to uncover these hidden gains in our free webinar.
Save your spot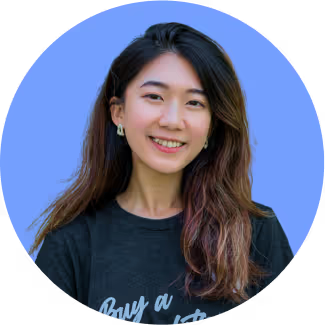
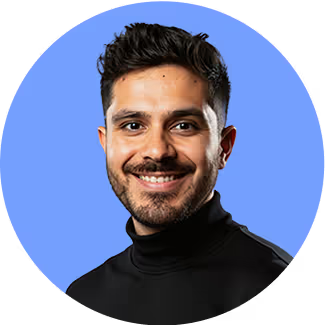