Table of Contents
Manual inspections. Unplanned downtime. Rigid production schedules. If these challenges make up your day-to-day life on the production floor, you’re not alone.
Traditional manufacturing processes often leave little room for speed or scale, but AI is changing the game for good. From smarter quality control to real-time production optimization, artificial intelligence is helping processing plants run leaner, faster, and more intelligently.
This blog breaks down how AI-powered process optimization works and where to apply it first, so you can predict failures before they happen and keep your operations one step ahead.
Why is process optimization important?
In the manufacturing industry, even tiny operational errors can lead to big losses.
Process optimization ensures that your team, tools, and data are used to their full potential. This means that your process will run smoothly and everything will improve. Output increases, costs go down, and your team spends less time on avoidable rework. It also means higher-quality outcomes.
It’s not just about doing things faster. It’s about building a smarter and more agile business that can adapt to change, scale quickly, and explore new opportunities without the usual friction.
Deloitte, McKinsey, and PwC on how AI revolutionizes manufacturing
- Deloitte reports that predictive maintenance can reduce unplanned downtime by 30–50%, increase labor productivity by 20%, and reduce inventory needs by up to 30%
- McKinsey estimates that predictive quality analytics using virtual sensors can reduce quality control costs by up to 50%, especially in regulated industries
- PwC reports that AI-enabled predictive maintenance can reduce maintenance costs by up to 25% and increase asset uptime by up to 20%
Top five use cases of AI-powered process optimization
AI is solving practical problems across production floors every day. Here are some use cases of how businesses are leveraging AI to optimize production processes:
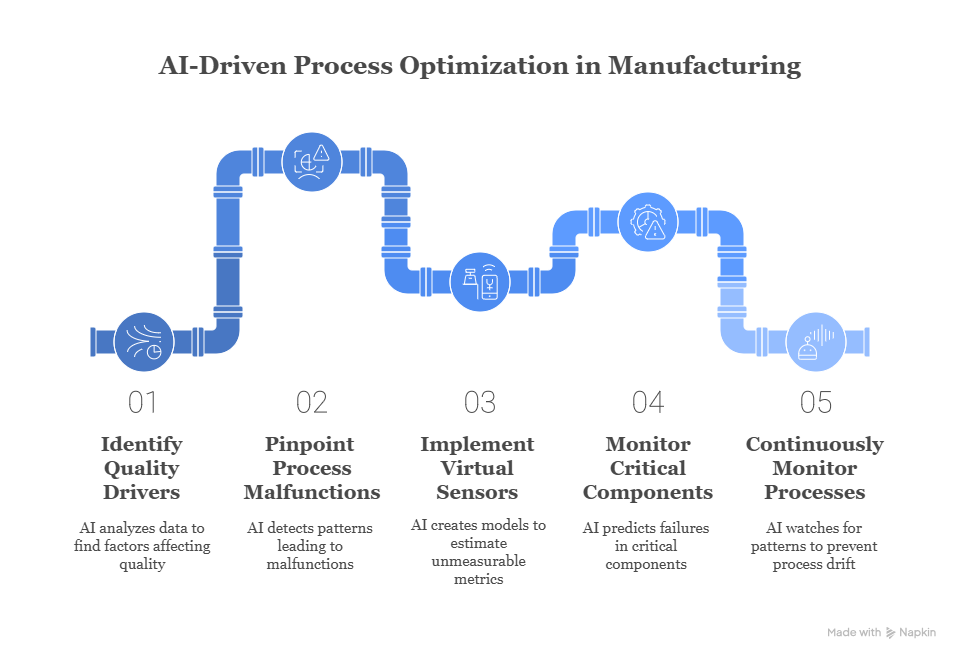
1. Discovering what drives quality: Process signal dependency analysis
In manufacturing, quality is king. But it’s not always obvious what’s causing your best (or worst) results. Sometimes, quality can only be measured after production through lab tests or inspections.
AI helps you predict quality issues before they happen.
By analyzing historical process data (like temperatures, pressures, or machine speed), AI identifies which parameters most affect product quality. It looks beyond the usual suspects and uncovers hidden dependencies between process variables and quality outcomes.
Why it matters:
Instead of acting on impulse or assumptions, you can refine process specifications based on real data and course-correct in real time, rather than waiting for batch-level failures.
2. Pinpointing what’s going wrong: Process malfunction analysis
Production issues are a fact of life, but the cause isn’t always clear.
When machines stop, temperatures spike, or when processes go out of spec, your team is often left guessing what went wrong. AI flips that script.
By analyzing historical data, AI identifies the exact patterns and conditions that led up to a malfunction. It compares these to normal operations and highlights what changed. It could be a sensor drift, a lag in valve response, or an operator adjustment.
Why it matters:
Instead of firefighting the same problems, your teams can proactively eliminate the root cause for process malfunctions and maintain smoother operations easily.
3. Seeing the unseen: Virtual sensors
Not every important metric in production can be measured directly. Some are too expensive to track in real time, some are hidden deep within the process, and others (like product quality) can only be confirmed after lab tests. That’s where virtual sensors come in.
A virtual sensor is a smart software model that estimates a value like temperature, pressure, or even product quality based on data from other sensors.
This “invisible sensor” fills the gap when you can’t measure something directly.
Let’s say you want to know the moisture content in a material, but there’s no sensor on the line that can measure it in real time. A virtual sensor can learn from past data by correlating variables like heat, flow rate, and humidity, and use those patterns to predict the moisture level every second.
Why it matters:
Virtual sensors let you monitor critical quality attributes instantly, even if they’re not directly measurable. That means quicker adjustments, fewer delays, and fewer surprises, making your process faster, leaner, and more resilient.
4. Predict before you break: Monitoring critical components
Standard monitoring systems check if equipment is working within set limits. But what if your system is about to fail even though everything looks normal?
This is where AI-based predictive monitoring shines.
AI models learn what “normal” looks like for a component based on vibration, temperature, current draw, and other signals. Then, they look for subtle changes or patterns that signal early signs of failure, long before alarms go off.
Why it matters:
This approach works especially well for components like motors, pumps, and valves that are cheap individually, but exist in huge numbers across plants. AI doesn’t just tell you when something's wrong; it buys you time to fix it before it fails.
5. Keeping things on track: Continuous process monitoring
Some problems in production can be fixed once and they’re gone. But others are more slippery as they pop up again and again unless you're constantly on watch.
AI process monitoring helps by identifying the “bad scenarios” and suggesting countermeasures. Next, a monitoring model watches for those patterns in real time and alerts operators when conditions begin to drift in that direction so they can intervene before the process spirals.
Why it matters:
This is problem-solving at its best. Instead of chasing issues, you prevent them. It’s a powerful tool for industries where process stability is key: like metals, semiconductors, and chemicals.
Challenges in traditional manufacturing processes
Manufacturing has come a long way, but many traditional setups still struggle with inefficiencies that eat into profits, slow down production, and limit growth. Here are the three most common (and costly) challenges manufacturers face and why overcoming them is critical to stay competitive.
1. Quality control and defect management
In traditional manufacturing, quality control often depends on manual inspections or spot checks.
That might work on a small scale, but when production scales, human error creeps in, and defects get missed.
In the automotive sector, a single defective part can trigger a mass recall costing millions.
Why it’s a problem:
Manual processes can’t keep up with the volume, speed, or complexity of modern manufacturing. And by the time you catch a defect, you’ve wasted materials, delayed timelines, and damaged customer trust.
Curious to learn how AI reduces manufacturing costs?
Read Blog
2. Waste and inefficiency
In many manufacturing setups, inefficiency hides in plain sight.
Machines run on fixed schedules, regardless of real-time demand. Teams follow outdated workflows because “it’s always been done that way.” This results in wasted materials, bloated energy bills, unnecessary labor, and slow turnaround times.
These inefficiencies stem from fragmented systems, aging equipment, and processes that can’t self-adjust. Instead of optimizing resources based on actual performance or usage data, manufacturers rely on assumptions or routine. And every assumption costs money.
Why it’s a problem:
You may not notice inefficiencies day to day, but it drains your bottom line. Wasted time means slower deliveries. Wasted materials mean lower margins. And wasted effort demoralizes your teams.
3. Limited scale and flexibility
Today’s customers want personalization, faster delivery, and more options. But traditional manufacturing systems were built for mass production, not for speed or variety.
Rigid workflows and static supply chains make it hard to switch gears. Launching a new product line or customizing orders often requires manual reconfiguration, retraining teams, or even buying new equipment, all of which take time and money.
Why it’s a problem:
Markets shift fast. If you can’t respond in time by scaling up or down, launching something new, or customizing production, you lose opportunities and fall behind.
Benefits of ensuring plant optimization with artificial intelligence
From smarter quality checks to predictive maintenance, here’s how AI helps optimize your operations while saving time, cost, and headaches:
1. Smarter quality control without slowing you down
AI uses computer vision and machine learning to scan thousands of products in real time, spotting even the tiniest defects that human eyes often miss. It identifies micro-cracks or misalignments before they cause a larger failure in electronics or auto parts — without adding more time or labor to the process.
Curious to learn how AI drives quality, reduces defects, and boosts efficiency in manufacturing?
Read Blog
2. Intelligent production scheduling
AI both automates and optimizes. Instead of relying on fixed schedules, AI can pull from live data to build smarter production plans. When a sudden supply chain delay hits, AI reshuffles priorities, redirects tasks, and minimize downtime to keep production on track instead of bringing the line to a halt.
3. Predictive maintenance
AI monitors vibrations, temperature, and usage in real time and alerts you before something breaks. This way, you fix issues proactively, reduce downtime, and extend equipment life. It’s like having a mechanic who knows what’s going wrong before you do.
4. Real-time insights that drive better decisions
You don’t need a data scientist to understand what’s working or not. AI can process data, actively learn from it, and tell you where bottlenecks are forming, which shift is underperforming, or when a line is trending toward failure. With real-time dashboards and alerts, operations teams can act fast, improve efficiency, and keep things running smoothly, all from one interface.
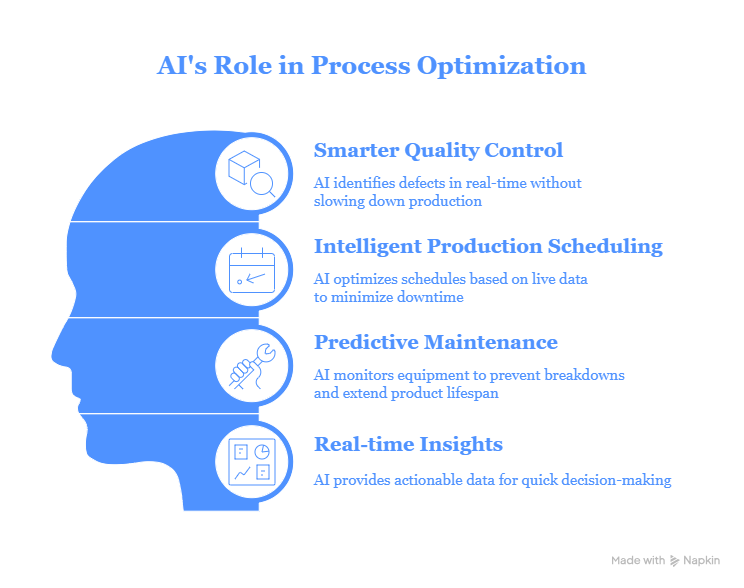
How to implement AI solutions in your processing plant
You don’t need to reinvent your entire tech stack to get started with AI. You just need the right tools, good data, and a clear path from pilot to scale. Here's how:
1. Choose the right AI tools for your use case
Start by identifying what problem you want to solve.
Different AI tools are good for different goals so look for tools that fit your goals and can work well with the systems you already use such as your ERP, CRM, or MES.
2. Get your data and systems ready
AI needs good data to work efficiently. Before you train your AI model, gather and clean the right kind of data. This might include:
- Machine logs that show when breakdowns happen
- Production data from past shifts
- Customer complaints or quality inspection results
Make sure your systems are connected. For example, your ERP system should be able to send data to your AI tool. This helps the AI work with complete, up-to-date information.
3. Train AI models with your actual data
Once your data is ready, train your AI model using actual products, machines, and process flows — and teach it to understand what’s “normal” and what’s not.
For example, a machine learning model trained on historical machine failure data can learn to predict future breakdowns. Similarly, a computer vision system can recognize what’s acceptable and what needs to be flagged after being trained on images of both good and defective products.
4. Test on a small process before going big
Don’t roll it out across the factory just yet. Start testing one line or one problem area.
If late deliveries cause trouble, try using AI to optimize your order scheduling on just one product line. Or if defects are high on one machine, run a pilot using computer vision just on that station.
This helps you measure how well the AI performs, gather feedback from your team, and identify what needs to be improved. Once you see faster cycle times, fewer errors, or better uptime, you can expand the solution to more parts of the business.
Power AI-driven optimization in your processing plant with 5X
5X helps manufacturers move from manual monitoring to truly intelligent plant operations.
By integrating data from SCADA systems, IoT sensors, and quality control tools, 5X gives teams a unified view of what's happening on the plant floor in real time with context. Its AI applications predict failures before they happen, optimize production schedules in real time, and adjust process parameters to maintain quality. This means fewer slowdowns, less waste, and higher throughput.
For example, in one deployment, 5X helped reduce plant-level waste by 25% and increased uptime with early maintenance alerts. The best part is that you don’t have to wait months to see results.
5X gets your first use case, like predictive maintenance or quality control automation, live within 48 hours. Built with Industry 4.0 in mind, 5X supports edge analytics, enterprise-grade security, and plant-floor agility for future-ready operations.
FAQs
Building a data platform doesn’t have to be hectic. Spending over four months and 20% dev time just to set up your data platform is ridiculous. Make 5X your data partner with faster setups, lower upfront costs, and 0% dev time. Let your data engineering team focus on actioning insights, not building infrastructure ;)
Book a free consultationHere are some next steps you can take:
- Want to see it in action? Request a free demo.
- Want more guidance on using Preset via 5X? Explore our Help Docs.
- Ready to consolidate your data pipeline? Chat with us now.
Get notified when a new article is released
Get an end-to-end use case built in 48 hours
Get an end-to-end use case built in 48 hours
How retail leaders unlock hidden profits and 10% margins
Retailers are sitting on untapped profit opportunities—through pricing, inventory, and procurement. Find out how to uncover these hidden gains in our free webinar.
Save your spot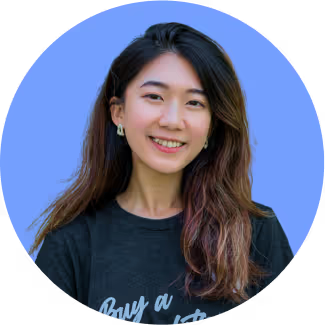
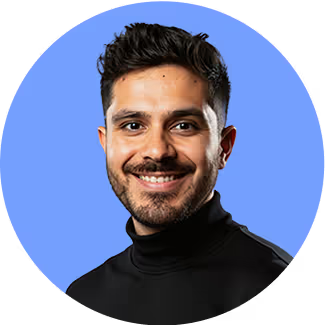